Hello Everyone,
As part of our process for developing a low-volume engine builds, we must get our rotary housings’ inner trochoid ground and lapped to a specific tolerance. Our designs require a less than [proprietary] variance in the epitrochoid of the rotor housing. (Sorry, I cannot share the details, this is information that is yet to be patented.) I will say that very few machine shops exist that can meet our specs. I only found one in Northern California. There was one in Los Angeles that did this work for Freedom Motors in the past, but they are out of business.
I’m taking a couple of our rotor housings (one below, surface coated but not yet ground) to the shop I contacted on Monday, so they can do the grind and we can verify their work. Just doing this grind will cost somewhere between $1000-$2000, but it’s the hardest and most critical part of production.
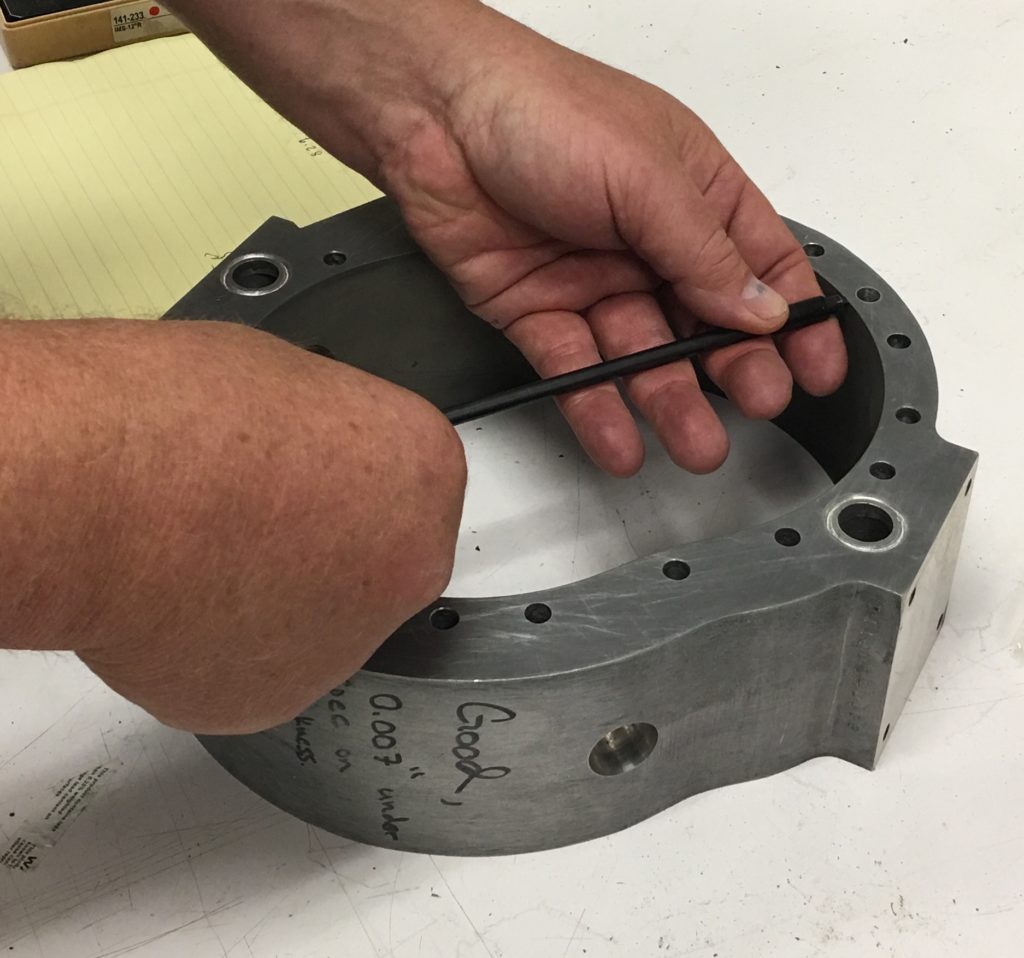
We have a large industrial rotary engine grinder that meets our specs (see pic below), but it requires industrial power (3-phase 480V) in order to run, and we don’t have that capability at our current site. So for now, we have to use a general machine shop that can do the surface grinding we need, and is also willing to do small numbers of housings. Many machine shops will not take R&D or low-volume jobs, just because of the amount of setup time on the mills.
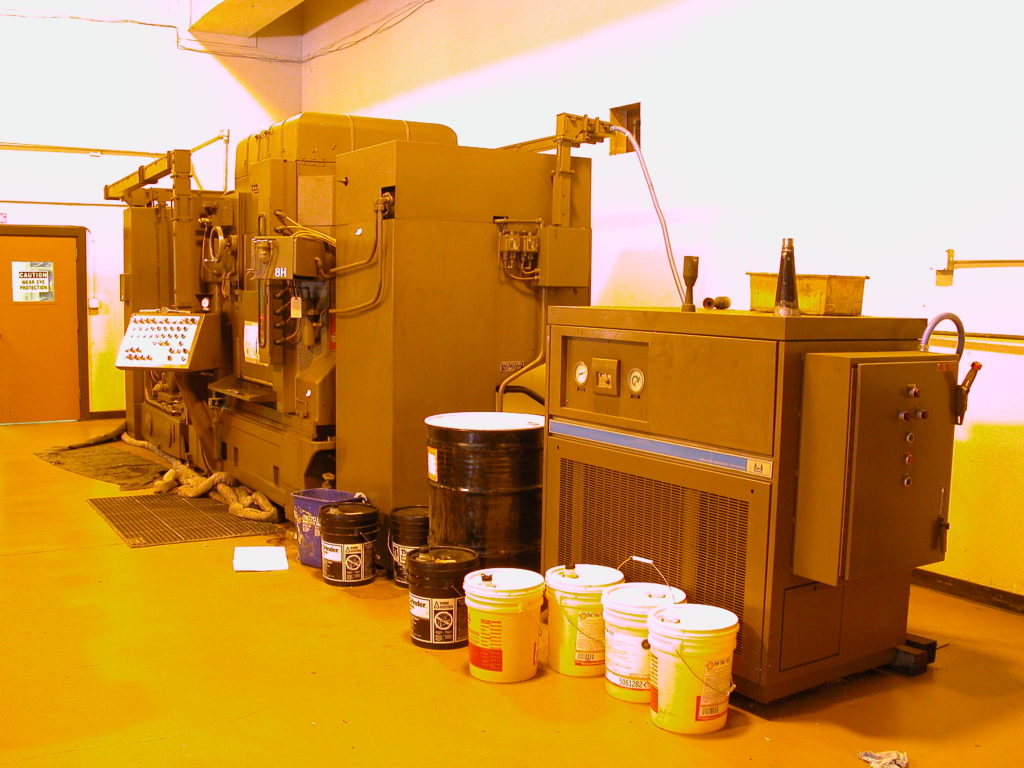
For more fun about the trochoids, including animations, check out this nice resource, which also has the formulas for generating the epitrochoid (or peritrochoid) coordinates of a Wankel rotary engine. They also provide a link to Kenichi Yamamoto’s book “Rotary Engine”
Best Regards – Dave